NASA Deep Space Food Challenge
The Future of Sustainable Food Production
Welcome to my dedicated page, where I proudly showcase my contributions to the NASA Deep Space Food Challenge, an exceptional competition where engineering and space exploration converge. Fueled by my passion for space exploration and driven by my founding role in the Auto Terra Project.

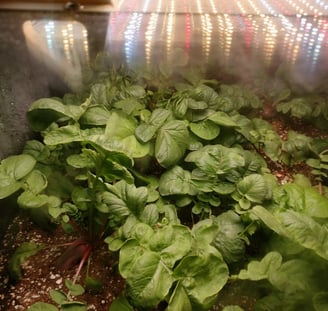
Necessity, The Mother of Invention
Stepping back to 2020, amid a global crisis, my co-founder and I were deeply moved by the stark reality of food insecurities' impact. We recognized that this crisis was further compounded by the disruptive impact of the pandemic. COVID-19's far-reaching consequences cast a shadow on food production, distribution, and access, revealing vulnerabilities such as empty supermarket shelves and disrupted supply chains. Determined to make a difference, we assembled a team to alleviate immediate distress and pave the way for a more secure, nourished future.
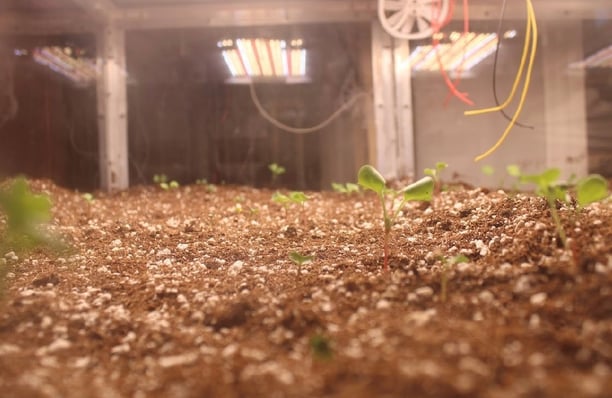
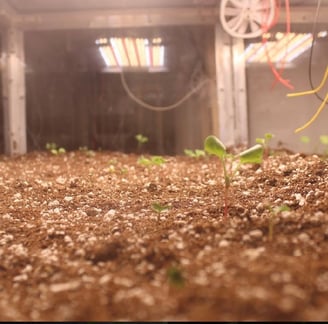
Making A Difference
Amidst the pandemic, we eagerly joined the UMass Lowell DifferenceMaker Program, harnessing its abundant resources to propel our project forward. This initiative granted us unparalleled access to industry experts, professors, scientists, and state-of-the-art laboratories. The DifferenceMaker Program not only propelled our project's growth but also nurtured our growth as emerging innovators, equipping us with a comprehensive skill set and connections that have fortified our journey toward transformative outcomes.
Design Phase
During the design phase within the DifferenceMaker program, we balanced the Deep Space Food Challenge's specific requirements with potential consumer market needs. Through multiple designs and iterations, we refined our solution using NASA's feedback and expert insights.
Beyond Phase 1
Advancing beyond Phase 1 of the competition was a significant milestone for us, a testament to the meticulous work we put into aligning our solution with the rigorous standards of the Deep Space Food Challenge. Our efforts were validated when NASA's review awarded our project a fantastic design rating, underscoring the thoroughness and innovation of our approach. The invaluable feedback we received from NASA further guided our path, allowing us to refine our solution with precision and purpose as we moved forward in the competition.
An Iterative Design, First Prototype
Navigating constraints in resources, we embraced agile development to construct our first prototype. Utilizing funds secured from the DifferenceMaker competition, we constructed a minimum viable product. With an eye on potential assumptions being incorrect, we swiftly built a full-scale model demonstrator, expediting testing and amassing crucial data to guide our iterative design approach.
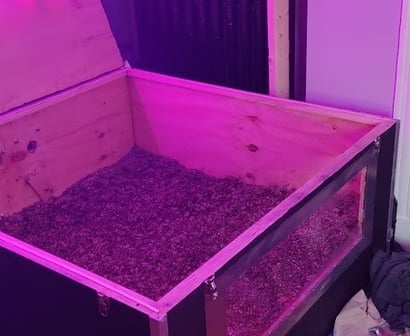
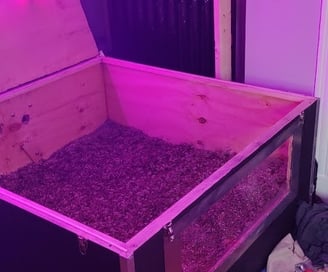
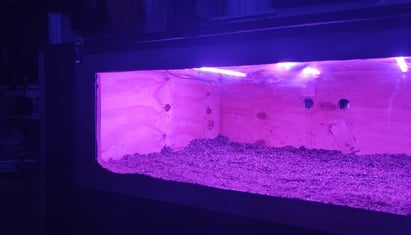
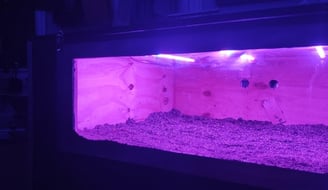
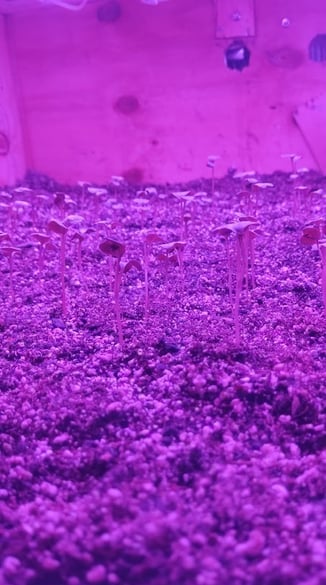
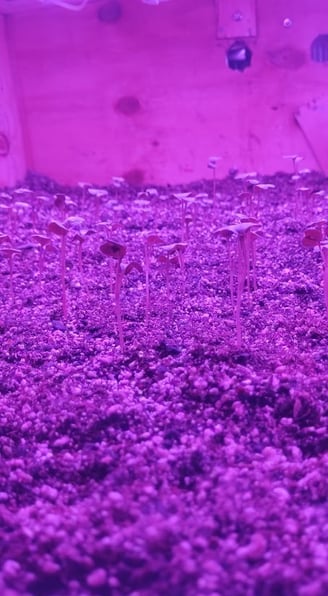
Successes, Failures, Lessons Learned
Prototype 1 yielded significant successes and invaluable lessons. Our proprietary soil-based substrate exceeded expectations, delivering optimal properties and nutrients while maintaining a lightweight composition. This facilitated robust plant growth and provided a wealth of data, enriched with valuable insights.
However, despite the successes there were notable failures. Inadequate air circulation negatively impacted produce conditioning and humidity control. Anticipating potential insufficiencies in the LED lighting, we chose to proceed with this setup due to budgetary constraints and a primary focus on agile development, aiming to establish a hardware proof of concept. Wood construction exhibited vulnerabilities as expected, with biological degradation, weight issues, and system imperfections.
These setbacks underscored the pressing need for improvements in air circulation, humidity control, lighting, and alternative construction materials. While the known limitations were deemed acceptable for initial data collection, addressing them became a top priority for subsequent iterations.
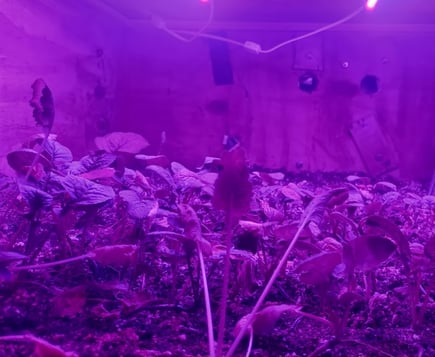
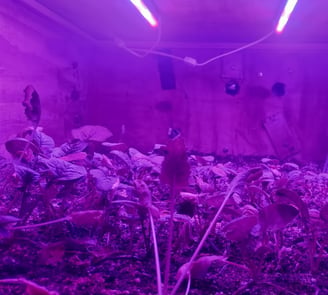
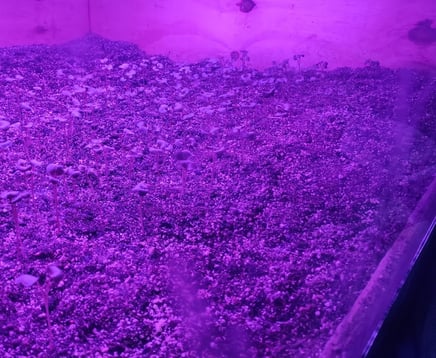
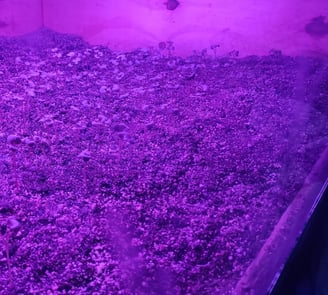
Modular Design Pathfinder, Second Prototype
The Second Prototype was a critical advancement, integrating modular aluminum extrusion and introducing novel materials. Expanding material options included food-safe plastics and FDA-approved RTV silicone while transitioning from glass to polycarbonate reduced weight and increased durability. Introducing a fabric-over-frame design enabled a collapsable enclosure for easy transit. Constructed at one-quarter scale in the x and y axes, this prototype facilitated comprehensive testing of our upgraded humidity and temperature control system, featuring enhanced air circulation and conditioning. It allowed rapid experimentation with electronics, hardware, lights, cooling, humidity control, and sensors. The scaled model also effectively tested fabric-over-frame and modular construction methods, refining design choices for future stages.
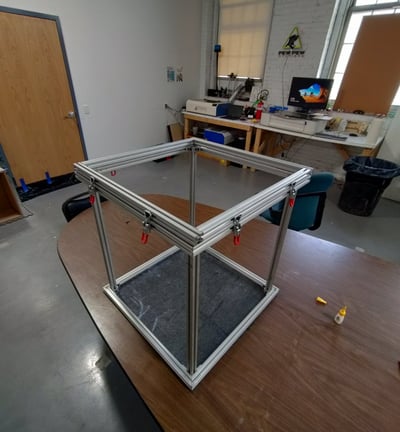
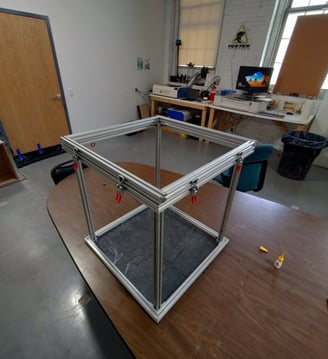
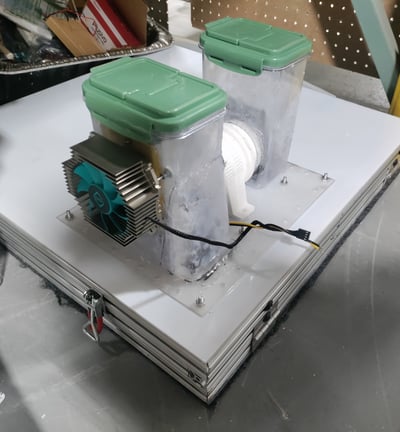
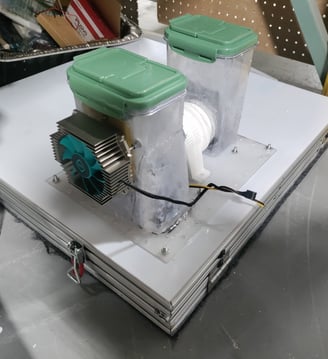
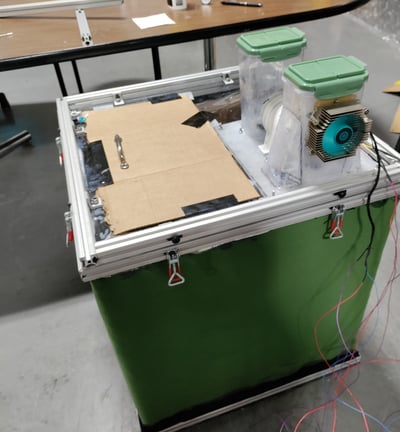
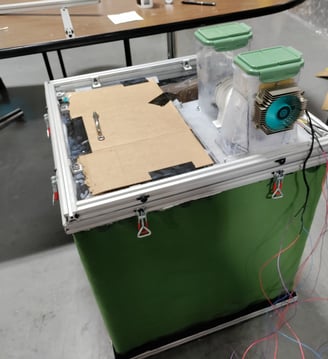

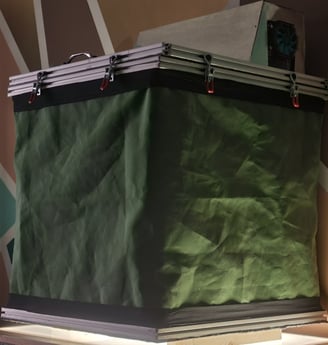
Pioneering Closed Ecosystem Solutions
The Second Prototype provided a pathway to future success through key innovations. It introduced a thermally separated lighting module to isolate LED-generated heat, while aluminum nanocoated reflective material enhanced lighting efficiency. Modular design enabled sensor and electronics swapping. Materials were rigorously tested for produce safety, crucial in a closed ecosystem environment. Challenges included refining complex construction methods for manufacturability, improving assembly efficiency, and addressing sensor resilience in corrosive environments. While challenges remain, this prototype illuminated the path toward an optimized closed ecosystem solution.
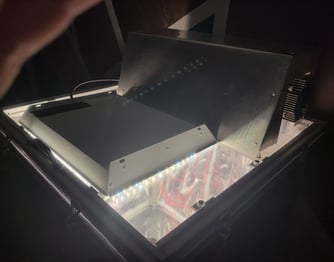
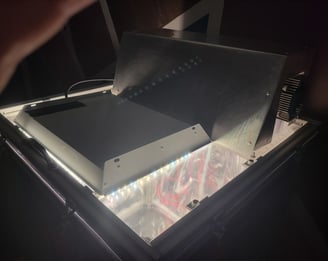
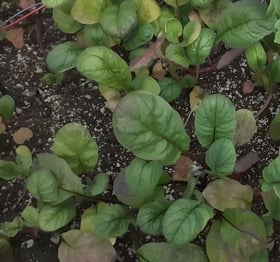
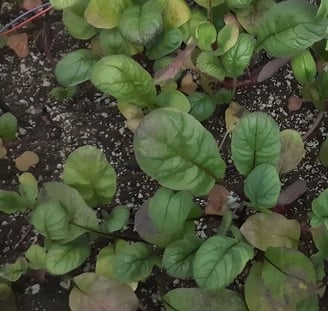
Gallery Of Second Prototype
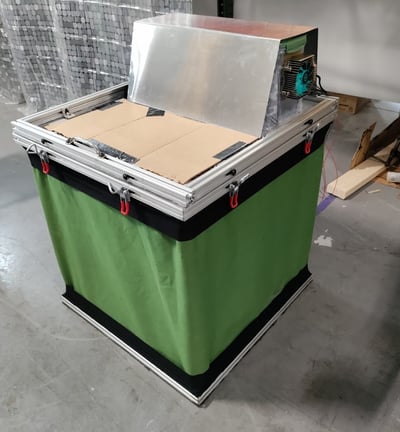
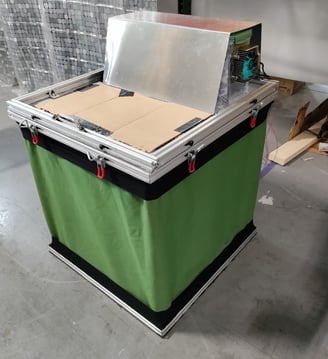
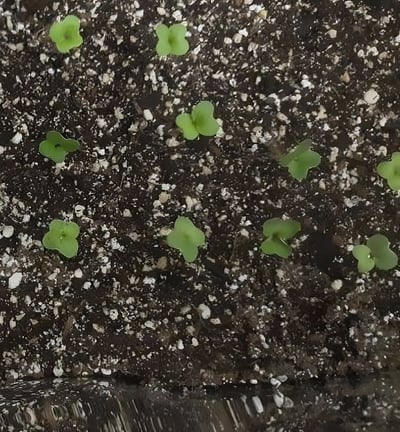
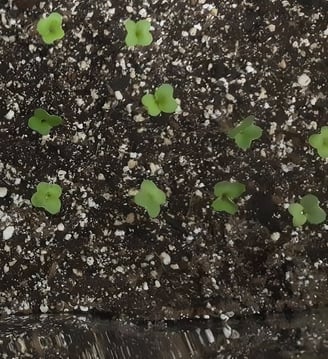
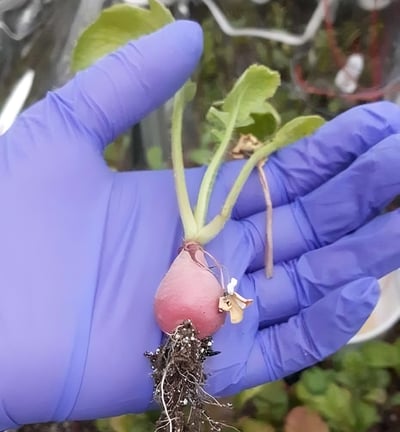
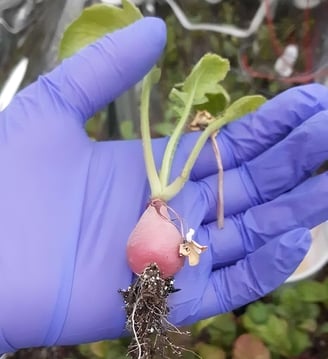
The Third Prototype represented a significant advancement. Engineered with a clear focus on future mass production, this iteration streamlined construction through additive manufacturing, combining modular construction and the use of food-safe polycarbonate. A unique custom modular airtight enclosure system allowed for easy expansion and adaptable cooling/conditioning adjustments. Polycarbonate panels provided real-time visual insight into soil and root propagation.
Key innovations encompassed a water-cooled humidity and temperature system, agnostic to cooling apparatus, and the integration of 3-phase brushless motors with external speed controllers for efficient fan control, without introducing harmful PCB materials. Extensive additive manufacturing enabled rapid prototyping.
The prototype also introduced robust sensors, mitigating corrosion concerns. Pushing boundaries, the Third Prototype laid a sturdy foundation for optimizing closed ecosystem solutions.
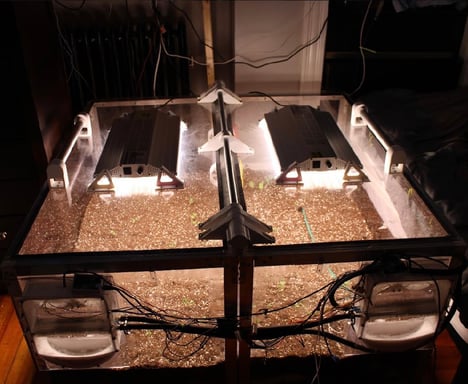
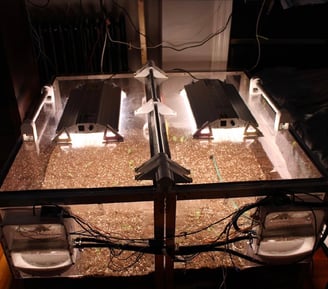
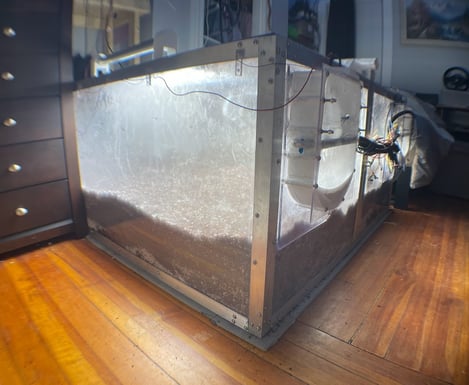
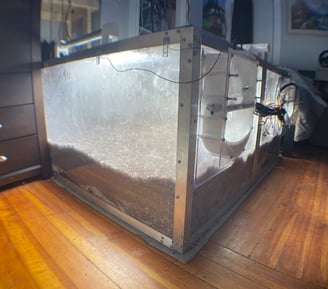
Streamlined Innovative Design, Final Prototype
A Strong Basis For Development
Built upon the robust foundation established by its two predecessors, the Third Prototype represents a significant milestone that builds upon prior innovations to propel our closed ecosystem solution forward. It strategically leverages the successes and lessons from previous iterations to introduce a host of new innovations.
Modular Construction Excellence: It introduces a custom modular airtight enclosure system, allowing easy expansion and customization of the internal environment.
Enhanced Cooling and Humidity Control: This iteration employs a thermally cooling-agnostic system, capable of utilizing various thermal removal methods, including a liquid-cooled solution, for efficient temperature and humidity regulation while reducing hardware contamination risk.
Efficient Fan Control: Utilizing 3-phase brushless motors with external speed controllers ensures efficient internal fan management without PCB material concerns.
Resilient Sensors: Advanced, corrosion-resistant sensors are introduced to thrive in the corrosive, high-moisture closed ecosystem.
Thermal Separation for LED Lights: LED lights are strategically positioned outside the system, using clear polycarbonate to transmit light while insulating excess heat, minimizing the load on cooling and humidity control systems.
These innovations, built upon prior successes and challenges, underscore the continuous commitment to improving our closed ecosystem solution and driving it toward optimization.
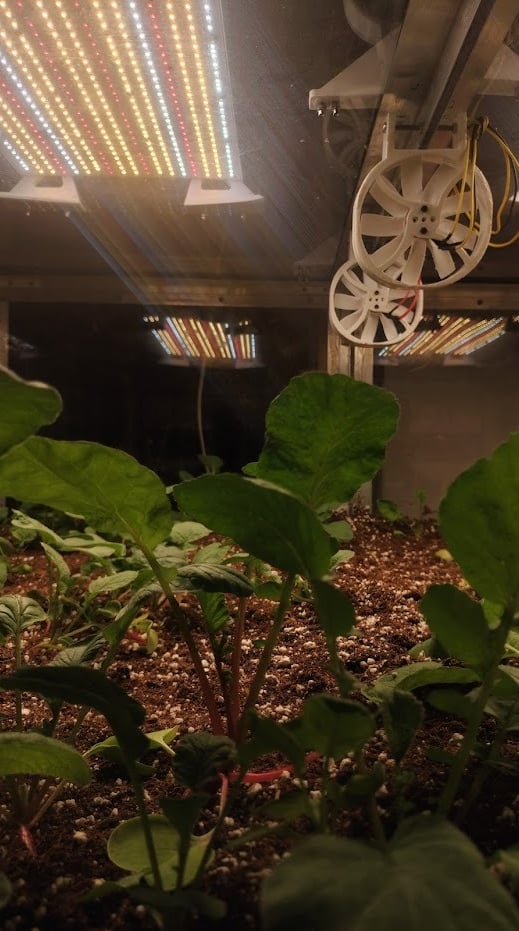
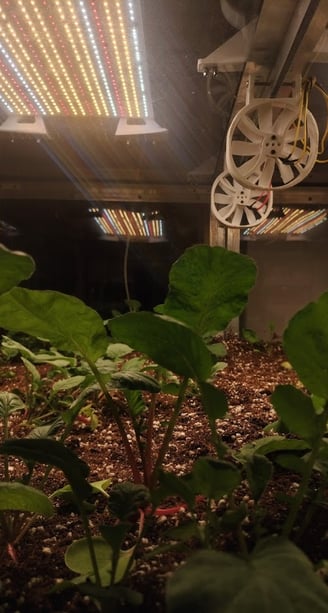
From Concept to Innovation, Novel Advancement Closed Ecosystems
The Third Prototype marks a significant milestone in our remarkable journey towards perfecting closed ecosystem solutions. From the very first prototype, where we embarked on this ambitious path, to the iterative enhancements of the Second Prototype, and now the Third Prototype's groundbreaking innovations, we've come a long way.
Our journey has been one of relentless dedication to pushing the boundaries of innovation. We've learned from challenges, celebrated successes, and always strived for improvement. The Third Prototype stands as a testament to our evolution, showcasing our capacity to adapt, learn, and innovate.
From modular construction to advanced thermal management and resilient sensor technology, we've embraced each lesson to create a more efficient, adaptable, and versatile closed ecosystem. This journey is far from over, but as we look back, we can take pride in how far we've come and the exciting path that lies ahead in the pursuit of self-sustaining ecosystems for the future of space exploration and sustainable living.
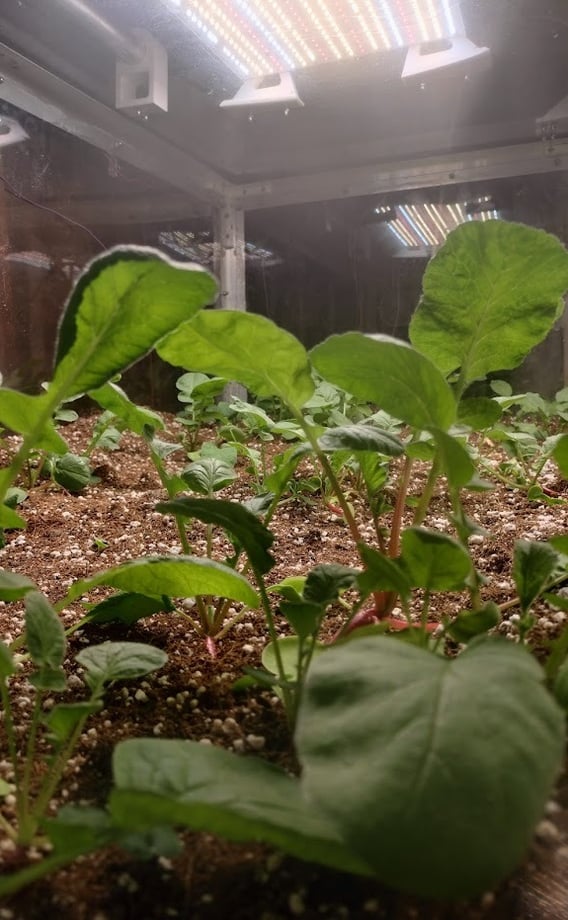
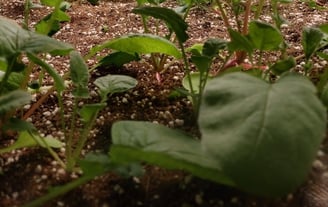
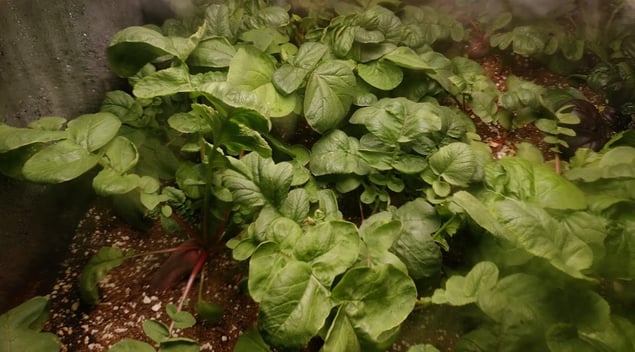
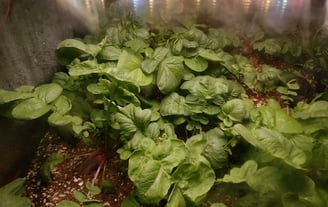